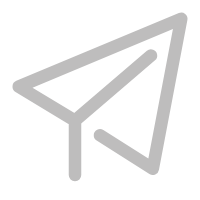
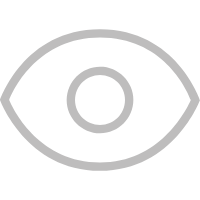
Since March 2017, the state has resolutely laid the "blue sky defense war", the treatment of volatile organic compounds (VOCs) pollution bears the brunt, and the coating industry, which is a major VOC emission emitter, has been pushed to the forefront of environmental protection.
The powder coating is a 100% solids, zero VOC "4E" coating. It has been recognized as an environmentally friendly coating since its inception and has quickly achieved subversive industrial replacement for solvent-based coatings in many traditional industrial fields, from traditional Furniture, home appliances, aluminum profiles, transportation, energy and other industries have achieved good results in the shipbuilding industry, marine engineering and pipeline industry. Powder coating has low environmental requirements, and can be used in a variety of coating methods such as fluidized bed, static electricity, roll coating, shower coating, flame, etc. The overspray powder can be 100% recycled, and the coating performance is excellent, which is a relatively fast development. VOC coating.
The data shows that in 2017, China's powder coating industry output reached 1.7 million tons, an increase of 13.4%. Because powder coatings are solvent-free, non-polluting, recyclable, environmentally friendly and energy-saving, they have quickly become the “new darling” of the industry. There are many large-scale coating companies planning to lay out the field of powder coatings with zero emissions of VOCs.
The advantages of powder coatings:
Powder coatings achieve zero waste and zero pollution during the manufacturing process, and the scrap produced in production can also be recycled.
Powder coating can meet the requirements of anti-corrosion and decoration in many fields, and the utilization rate of powder spraying is high.
The same thickness of paint film, powder coating coating area is more than double the traditional solvent-based coating.
From the cost point of view, the same capacity, powder coating companies' floor space and production costs are only half of the traditional solvent coating companies.
Among the several types of coatings currently in use, the price of powder coatings is also the lowest.
Powder coating
Exhibition direction
Heavy anti-corrosion field
China is the world's first country in the production and use of heavy-duty anti-corrosion coatings. In 2017, the total output of our national anti-corrosion coatings was about 6 million tons, of which the development prospect of heavy-duty anti-corrosion coatings was the most impressive. In the application of heavy anti-corrosion coatings such as ships, bridges and steel structures, solvent-based coatings are still the mainstream, accounting for more than 90% of wind-electric coatings. The demand for green coatings for onshore wind power and offshore wind power is very urgent.
Water-based coatings are difficult to completely replace solvent-based coatings, and powder coatings are expected to have a larger market share under the trend of green coating.
Special functional applications
Functional powder coatings include UV curable powder coatings, antibacterial mildew powder coatings, electrical insulating powder coatings, high temperature resistant powder coatings, anti-graffiti powder coatings, fine powder coatings, thermal transfer powder coatings, electrophoretic powder coatings, and the like.
Non-metallic substrate coating field
Conventional powder coatings are usually limited to metal substrates and are difficult to apply on non-metallic substrates such as concrete substrates, plastics, glass, etc. Some alloys cannot be coated with powders, such as magnesium alloys. In the field of non-metallic substrates, powder coating technology is difficult to break through in the short term. However, it is gratifying that UV-cured powder coatings and low-temperature curing powder coatings make it possible to apply powder coatings to non-metallic substrates. Powder coatings have a good borrowing effect in MDF applications.
On-site construction of very large components
Certain very large components (such as large tanks, platforms, decks, etc.) and non-metallic substrates for interior and exterior wall coatings or large concrete components can only be selected for liquid coatings suitable for on-site and ambient temperature applications. However, the development of future coating equipment may be able to achieve powder coating construction in the above fields, such as high-infrared heating technology, flame spraying technology or application of UV-curing powder coating, it is possible to achieve powder coating of large components, because of flame spraying and UV Curing does not necessitate heating the entire component.
Application of high precision materials
High-precision materials such as graphene and nanomaterials are difficult to be well dispersed in the conventional powder melt extrusion manufacturing process, and thus these excellent materials are difficult to impart a qualitative mutation to the powder coating.
It is reported that China's powder coating enterprises are mainly distributed in the coastal areas, the Yangtze River Delta, the Pearl River Delta and the Bohai Rim region. The sales of powder coatings in the three major coatings industry bases account for 94% of the country.
From the 10% market share of powder coatings, powder coatings meet the dual needs of environmental protection and the market, and have become the third largest coating after latex paints and solvent-based coatings.
But to further promote the rapid development of powder coatings, it is necessary to explore its weaknesses. If the curing temperature is successfully reduced, not only can the energy consumption be greatly reduced during the coating process, but also the powder coating can be applied to a wider range.
According to statistics, the annual use of paint in the country is about 25 million tons, the traditional solvent paint accounts for about 54%, and the powder paint accounts for about 10%. To further replace solvent-based coatings, it is necessary to increase the research and development of core technologies, formulate more stringent VOCs emission standards, and accelerate the upgrading and transformation of backward production capacity.