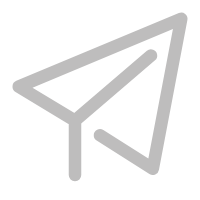
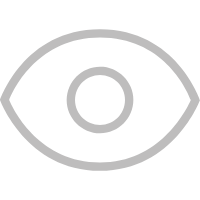
Color difference
Cause:
1. The thickness of the coating film is not uniform;
2. The temperature distribution of the curing oven is not uniform;
3. The workpieces of different materials, thicknesses, shapes and sizes are simultaneously produced and operated;
4. When replacing the color of the paint, if the powder supply device, spray gun, dusting room and powder coating are not cleaned;
5. The color difference caused by uneven distribution of powder pigments.
Solution:
1. Ensure uniform coating film thickness;
2. The temperature distribution of the curing furnace is uniform;
3. It should be classified according to the material, thickness, shape and size of the workpiece, and then set different baking time for baking and curing, which may reduce the color difference of the coating film;
4. When replacing the paint, clean the parts and try to stagger the materials with different color difference.
5, improve the quality of the powder, to ensure that the powder L, a, b phase difference is small and positive and negative.
Loss of light, yellowing
Cause:
1. The pigment of the powder coating itself is not resistant to high temperature or the high temperature of the resin material is easy to turn yellow;
2, the pre-treatment quality of the workpiece is poor, there are residues;
3, the curing time is too long or the curing temperature is too high, the local temperature is too high or too close to the heating tube;
4. Two different color or nature powders are mixed.
Solution:
1. Use high quality powder coating;
2. Wipe clean after pre-treatment, and clean debris before painting;
3. Select the appropriate curing temperature and time, and the curing furnace increases the hot air circulation to ensure the proper distance between the workpiece and the heat source;
4. Thoroughly clean the powder supply tank, recovery system, powder feeding pipe, spray gun, spray chamber and other devices when changing powder.
Impurities, particles
Cause:
1. Curing impurities in the furnace;
2. Dust in the dusting room, clothing fibers, equipment abrasive grains and dusting system;
3. Excessive powder additives, uneven pigment dispersion or too high temperature during powder production, some of the powder has been cross-linked and cured;
4. The powder coating is agglomerated and agglomerated, and the atomization is not good when it is ejected;
5. There are particles and debris on the surface before the profile is sprayed;
6. The recycled powder added is too much and has not been sieved;
7. The coating is too thin to spray, and the substrate is difficult to cover with slight disease.
Solution:
1. Thoroughly clean the inner wall of the curing oven with a damp cloth and a vacuum cleaner, focusing on the gap between the suspension chain and the duct;
2. Purge the dusting system with air before starting work every day, thoroughly clean the powder spraying equipment and the powder spraying room with a damp cloth and a vacuum cleaner;
3. Improve the quality of the powder;
4. Change the conditions of the warehouse, and use the expired plastic powder to transform the painting equipment;
5. Clean up before spraying, reduce the burrs of the profile, etc.;
6. The recycled powder added is suitable and should be sieved;
7. Appropriately increase the thickness of the coating.
cause:
1. Pre-treatment degreasing or uncleaning after degreasing causes surfactant residue;
2. The oil and water content in compressed air exceeds the standard;
3. The water content of the powder coating itself exceeds the standard or the raw material is unqualified, the volatile content exceeds the standard or the powder is damp;
4. The oil stain on the hanging chain will fall into the dusting room or the oven, which will also pollute the powder coating, the powder spraying room and the drying tunnel;
5. Shrinkage caused by mixing powder;
6. The spray gun is too close to the workpiece, causing electric shock perforation.
Solution:
1. Control the concentration of the oil removal tank, reduce the oil content of the profile and enhance the washing effect;
2. Increase the oil-water separator to achieve dry compressed air;
3. Use high-quality powder coating or improve powder storage and transportation conditions, increase dehumidifier to ensure timely use of recycled powder;
Clean the hanging chain in time to ensure that no oil is dropped;
4. Thoroughly clean the dusting system when changing powder;
5. Use a suitable distance (preferably 150-300mm) for dusting.
Cause:
1. The surface of the workpiece is too rough, and the coating is difficult to level;
2. The powder particle size is too coarse or the self-leveling property is poor;
3, the coating is too thin or too thick, when it is too thin, it is muscle-like wrinkles, when it is too thick, it is marked with orange peel;
4, electrostatic shielding, coating film thickness is not uniform; 5. curing temperature is too low, not fully leveling.
Solution:
1. The surface is refined by sanding and other methods, and the coating is suitably thicker;
2. Use high quality powder coating;
3. Master the powder amount and spraying time to ensure the appropriate thickness (40-60μm);
4. Improve the spray gun, reduce the static shielding area as much as possible or use the friction type spray gun;
5, increase the curing temperature, extend the leveling time 110-135 ° C for the melt leveling area, this area should be warmed slowly, time 8-10 is easy.
Cause:
1. The voltage is too low when spraying;
2. The grounding condition of the workpiece is not good;
3. The high voltage generator resistance is too small and the output current is too large;
4, the dust pressure is too large;
5, the hook insulation, the conductivity is too poor;
6. The spray gun is too far away from the workpiece;
7. Poor powder properties.
Solution:
1. Adjust the voltage to an appropriate value of 60-90KV;
2. Add ground wire to ensure good grounding;
3. Appropriately increase the resistance of the resistor;
4. Appropriately reduce the pressure of the powder supply;
5. Regularly clean the hooks to make the conductivity good;
6. Adjust the distance of the spray gun properly;
7. Use high quality powder coating.