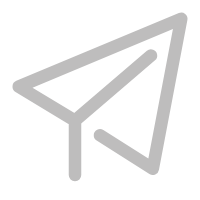
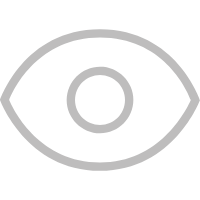
Factors affecting gloss and gloss
Determination of gloss and gloss
When light is projected onto the surface of an object, light is reflected. The ability of the surface of the object to reflect light is called gloss. The gloss of the surface of different objects is different. The measure of the ability of the surface of the object to reflect light is called glossiness. Gloss is expressed as a percentage. The higher the gloss of the surface of the object, the stronger its ability to reflect light and the higher the brightness. The size of the gloss was measured by a photoelectric gloss meter. Depending on the degree of gloss, the coating can be classified into bright, matt, matt, and the like.
Factors affecting gloss
Coating surface roughness
The surface gloss of the object is closely related to the roughness of the surface of the object. When light hits the surface of the object, part of it is absorbed by the object, part of it will be reflected and scattered, and some will be refracted. The smaller the roughness of the surface of the object, the more light is reflected and the higher the gloss. On the contrary, if the surface of the object is uneven, the amount of light scattered is increased, resulting in a decrease in gloss.
Coating film formation process
After the paint is applied to the surface of the object, it is solidified into a film by evaporation of the solvent. The formation of the coating film is critical to the surface roughness and gloss of the coating. In the wet film stage, the diffusion rate of the solvent is controlled on the surface of the coating film. When the evaporation rate of each component of the solvent is not much different, it is possible to obtain a high-gloss surface; otherwise, when the components of the solvent are in the wet film stage When the volatilization rate is different, it tends to form a curl or even precipitate out of the polymer molecules, and becomes a particle or agglomerate of different sizes, and the surface of the coating film is uneven. In the dry film stage, the evaporation rate of the solvent is mainly controlled by the diffusion of the solvent in the entire coating film, and also affects the roughness of the surface of the coating film. In addition, during the formation of the coating film, as the solvent evaporates, the coating film becomes thinner and shrinks, and some suspended heavy particles in the coating are rearranged on the surface of the coating film, causing the surface of the coating film to be uneven.
Particle size and distribution of pigments and fines
The particle size and particle size distribution of the pigment and filler in the coating are one of the important factors affecting the gloss of the coating film. When the diameter of the pigment particles is less than 0.3 μm, a high gloss coating film can be obtained. The reason is that the pigment particles dispersed in the coating are made into a coating film of a certain thickness, and after drying, only the uppermost pigment particles are locally protruded, and the surface roughness of the coating film caused by the pigment ions having a particle diameter of less than 0.3 μm is caused. Will not exceed 0.1μm. When the average particle diameter of the pigment is between 3-5 μm, a coating film having a good matting effect can be obtained.
In addition to the above three factors can affect the gloss of the surface of the coating film, the volume concentration of the pigment (PVC), the dispersibility of the pigment, and the surface structure and surface reflection characteristics of the coating film also affect the gloss of the surface of the coating film. Among them, as the PVC of the pigment increases, the gloss of the surface of the coating film first decreases, and a minimum value occurs at the limit volume concentration (CPVC) of the pigment, and then the gloss increases as the PVC increases. When the type and amount of the pigment are determined, the better the dispersion, the higher the gloss of the surface of the coating film.
Extinction principle
In combination with the mechanism of the gloss of the surface of the coating film and the factors affecting the gloss, the extinction is to use various means to destroy the smoothness of the coating film, increase the surface micro-roughness of the coating film, and reduce the reflection of light on the surface of the coating film. Can be divided into physical extinction and chemical extinction two ways. Physical matting is the addition of a matting agent, which causes the coating to be uneven during the film formation process, increasing the scattering of light and reducing reflection. Chemical extinction relies on the introduction of structures or groups such as polypropylene grafted species that absorb light into the coating to achieve low gloss.
Extinction method
Matting agent
(1) Metal soap
Metal soap is a kind of matting agent commonly used in the early days, mainly some metal stearates, such as aluminum stearate, zinc stearate, calcium stearate, magnesium stearate, etc., among which aluminum stearate is the most . The extinction principle of metal soap is based on its incompatibility with the coating composition. It is suspended in the coating with very fine particles. When it is formed into a film, it is distributed on the surface of the coating film, which causes microscopic roughness on the surface of the coating film and reduces the surface light of the coating film. The reflection achieves the purpose of extinction.
(2) Wax
Wax is a matting agent that is widely used earlier and is an organic suspension type matting agent. After the coating is completed, the wax in the coating film is deposited with the volatilization of the solvent, and the fine crystal is suspended on the surface of the coating film to form a roughness surface of the scattered light to eliminate the light. Wax as a matting agent is characterized by its ease of use and imparts a good hand and water resistance, damp heat resistance and stain resistance. However, after the wax layer is formed on the surface of the coating film, the volatilization of the solvent and the infiltration of oxygen are prevented, which affects the drying and coating of the coating film. The future development trend is to synthesize polymer wax and silica to achieve the best extinction effect.
(3) Functional type fine material
Inorganic pigments, such as diatomaceous earth, kaolin, synthetic silica, etc., are functional fine materials specifically used as matting agents, and are inorganic-filled matting agents. When the coating film is dry, their tiny particles will form a slightly rough surface on the surface of the coating film, reducing the reflection of light to obtain a matte appearance. The matting effect of such matting agents is subject to many factors.
Taking silica as an example, when it is used as a matting agent, its pore volume, average particle size and particle size distribution, dry film thickness and whether the particle surface is treated or not, etc., will affect its matting effect.
In order to obtain low gloss, the matting agent plays an irreplaceable role. However, in the course of use, there are still many defects to be improved, such as the selection and use conditions of the matting agent are relatively harsh, and the price is high. Domestic matting agents mostly contain cyclic anthraquinones, and the coating film is easy to yellow and has poor baking resistance. A matting agent with a good production performance and a moderate price is still a problem to be solved.
Matting resin
When the resin is an indispensable component of the coating, a matting resin is produced, and it is used to form a film with other resins to obtain a low gloss. The use of matting agents can be avoided and coating costs can be reduced.
Its mechanism:
(1) The use of the functional group in the matting resin and the curing agent in the coating composition differs from the curing temperature of the other resin to cause sequential curing, which causes uneven shrinkage on the surface of the coating film, thereby destroying the smoothness of the surface of the coating film and producing matting.
2 Increasing the difference in surface tension between the two resins, resulting in uneven shrinkage of the coating film to produce micro-roughness.
(3) Introducing poorly compatible monomers into the synthetic resin, and coating the film to cause the synthetic resin to precipitate from the coating film, thereby increasing the microscopic roughness of the surface of the coating film and reducing the gloss.