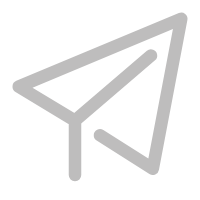
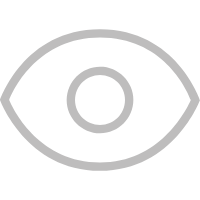
First, why should we test the salt spray test?
l In order to verify whether the metal parts on the product are exposed to the atmosphere or other environment, it may be corroded. The product can be placed in the use environment for a long enough time, such as a product life cycle. This is time consuming and laborious, in practice Medium is rarely used.
l This requires a convenient way to evaluate the corrosion resistance of the product.
l Salt spray test is an accelerated corrosion evaluation method for artificial atmosphere. It atomizes a certain concentration of salt water and then sprays it in a closed incubator to observe changes in the sample after being placed in the box for a period of time. To reflect the corrosion resistance of the sample to be tested. It is an accelerated test method, which is short-lived, does not require several years, only takes a few days, or even hours.
l Although the salt spray test is an effective test method, but due to many factors affecting corrosion, a single salt spray resistance cannot be used as a representative of other media, so the salt spray test results cannot be used as the test material in all environments. A direct guide to corrosion resistance. At the same time, the performance of the material in the test cannot be used as a direct guide to corrosion resistance during use.
l Nevertheless, the salt spray test method can still be used as a method to test the material.
Second, which products need to do salt spray test
l Metal and its alloys
l metal cover
l organic cover
l Anodized film
Third, the cover layer
1) Overlay type
l Organic coatings such as paints, varnishes, powder coatings, rust preventive oils, etc.
l Metal coating, such as electroplating, electroless plating, ion plating, sputtering, hot dip plating, chemical vapor deposition, etc. Commonly used plating layers are galvanized, copper-plated, nickel-plated, chrome-plated, tin-plated and brass-plated, lead-tin alloy.
2) Overlay effect
l Aesthetics For example: bright chrome plating
l Protect the base metal from corrosion
Fourth, the salt spray test test method classification
v Neutral salt spray test (NSS)
v Acetate spray test (AASS)
v Copper accelerated acetate spray test (CASS)
Common standard types: ISO 9227:2006 Europe (including UK)
ASTM B117-03 United States
DIN 50021:1988 Germany
(1) Neutral Salt Spray Test NSS (Neutral Salt Spray)
2 test standard selection
ISO 9227:2006 Europe (including UK)
ASTM B117-03 United States
DIN 50021:1988 Germany
The conditions of several test standards are the same, see the following
2 test conditions
Sodium chloride solution concentration 50g / L ± 5g / L
PH value is 6.5~7.2
Test chamber temperature 35 ± 2 ° C
(US 35+1.1/-1.7 °C)
Salt spray settling speed is 1.5±0.5mL per 80cm2 per hour
2 Sample preparation
The type, quantity, shape and size of the sample shall be determined according to the product standard. If no standard is met, the parties concerned shall negotiate.
The sample must be cleaned by appropriate methods before the test, but the protective organic film intentionally coated on the sample should not be washed away.
For the cut sample, apply the paint, paraffin or tape to protect the cutting area.
2 sample placement
The sample is placed in a salt spray box with the test surface facing up, so that the salt spray can settle freely on the test surface, and the test surface cannot be directly sprayed by salt spray.
The surface of the test specimen should be 20 degrees from the vertical direction.
The specimens may be placed on different horizontal surfaces of the tank, but they shall not be in contact with each other or in contact with the tank. The droplets on the specimen shall not fall on other specimens.
The sample holder is made of glass, plastic, etc. The material of the hanging sample cannot be made of metal, but the insulating material such as fiber is applied.
2 test time
The test time is determined according to different product specifications, generally 2/4/6/8/24 hours, more than 24 hours is an integral multiple of 24 hours.
E.g:
²Sample processing after test
After the test, the sample is taken out, naturally dried in the room for 0.5 to 1 hour, and then gently rinsed with clean flowing water at a temperature not higher than 40 degrees Celsius to remove the residual salt spray solution, and then blow dry immediately.
V. Sample rating
l Rating criteria selection
l Some proper noun explanation
Anode plating: Refers to the coating that the anode layer is anodized to the substrate. That is, the coating layer is more active than the substrate metal. If an electrochemical reaction occurs, the coating layer is first corroded. For example, steel is galvanized.
Cathodic coating: refers to the coating of the coating layer on the substrate. That is, the coating layer is less active than the substrate metal. If an electrochemical reaction occurs, the base metal is corroded first. For example, tin plating on steel.
l ASTM D610-01
The result of the assessment generally consists of a number and a letter, such as 6-S, 4-P. The front number indicates the corrosion area, and the back letters indicate the corrosion pattern. The specific explanation is as follows:
The corrosion pattern is as follows;
S Spot Rusting Several large pieces of corrosion
G General Rusting has large and small corrosion
P Pinpoint Rusting tiny pitting
H Hybrid Rusting mixed corrosion of several forms
图示如下:
l ISO 4628-3:2003
The result of the assessment is Ri followed by an Arabic number, such as Ri6, Ri4. Number indicates corrosion area
The correspondence between numbers and corrosion areas is as follows:
Rating number Corrosion area
Ri 0 0
Ri 1 0.05
Ri 2 0.5
Ri 3 1
Ri 4 8
Ri 5 40/50
l ISO 10289:1999
The assessment results generally consist of a protection rating (Rp) and an appearance rating (RA), if only a protection rating is required. Appearance rating can be omitted.
The protection rating (Rp) indicates the ability of the coating to protect the base metal from corrosion. It is usually represented by an alphanumeric number from 0 to 10. This number represents the area of corrosion of the base metal.
The appearance rating number (RA) indicates the extent of damage to the overlay. It usually consists of an Arabic number from 0 to 10 plus a lowercase letter and a capital letter. For example, 6 m A, 4 s C. In the above ratings, the Arabic numerals represent the corresponding cover damage area. The lowercase letters represent the subjective evaluation of the degree of damage of the cover layer, and the uppercase letters represent the type of cover damage.
(Rp, Ra explains
R=Rating
p = protection
a = appearance appearance)
The correspondence between the number and the corrosion area is as follows:
Subjective evaluation of the degree of damage of the cover layer
Vs = very mild
s = mild
m = moderate
x = severe
Classification of cover damage types
A Spot and/or color change caused by damage to the cover layer
B is very ugly to see the darkness caused by the corrosion of the cover layer that is not even visible.
C Corrosion products of the anode coating
D Corrosion products of cathodic coating
E surface pitting
F broken, peeled, peeled off
G bubbling
H cracking
I crack
J chicken claw or star defect
Rating example 1
Slight rust over 1% of surface, less than 2.5% of surface
Rp = 5
Very small surface eclips cause the entire surface to be slightly dark
Ra = 0 s B , vs E.
Rating example 2
Base metal corrosion occurred in 0.3% of the area of the sample
Rp = 7
The corrosion product of the anodic blanket covers a total area of 0.15%, and the area of the uppermost electrodeposited layer that appears to be slightly bubbling exceeds 0.75% of the total area.
Ra = 8 vs C, 6 m G
Rating legend: